New All-Electric Capri and Explorer Event
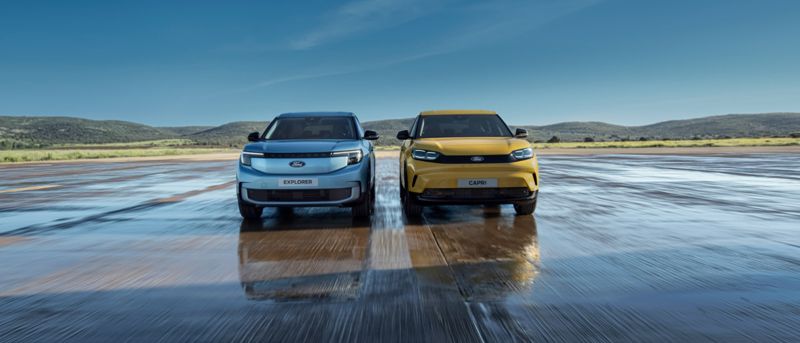
By the end of the year, the first fully electric volume model from Ford in Europe will roll off the assembly line in Cologne. Ford is not only converting its production facilities for the Cologne Electrification Center in preparation, it is also making production processes even more efficient and sustainable, driving digitization and Industry 4.0 in the process.
The latest innovation is the opening of a new 3D printing centre. Here, twelve high-tech 3D printers produce a wide variety of plastic and metal components from just a few centimeters in length and weighing as little as 30 grams, to others - produced by the centre's largest 3D printer – measuring up to 2.4 metres long, 1.2 metres wide and 1 metre high, and weighing 15 kilograms.
"We primarily produce tools and fixtures for our manufacturing areas here," said Nurah Al-Haj-Mustafa, Ford engineer for 3D printing. "Each part can be absolutely unique. Nevertheless, every print is the same in terms of quality and properties." These are, for example, measuring gauges for checking dimensions, templates for attaching the Ford logo, and in the future also massive gripper constructions as attachments for robots in body shell construction. Components for pilot and small series vehicles can also be printed in the new 3D printing centre.
Aside from the flexibility of 3D printing it can also save time and money with small quantities – up to 80 per cent compared to the conventional injection molding process, in which the production of the respective mold is very complex. There is also a sustainability aspect; 3D printing requires significantly less material and the shredded granules can be reused. The Manufacturing and Materials team at the Ford Research and Innovation Center in Aachen is currently working on a pilot project for the recycling of granulate for 3D printing.
The 3D printing process has been around at Ford in Cologne for a long time. As early as the 1990s, engineers at the Merkenich development centre began to 3D print components for test vehicles and prototypes. Ford set standards in this area of additive manufacturing. In 2019, for example, the Ford Research and Innovation Center was able to produce the largest metal part ever made using 3D printing. This was an aluminum intake manifold for the engine of a Ford F-150 converted by the late drifting legend Ken Block.
At Ford’s Valencia plant in Spain they have a dedicated team at its 3D printing lab who have created a catalogue of 5,000 printable parts that offer solutions for various stages of the plant’s manufacturing process. During 2021 alone, the department successfully created a total of 20,000 printed parts, with employees able to request or propose new parts when needed.
3D printing center already producing parts for upcoming E-model production
What is new and special about the 3D printing centre in Cologne is the networking with the other areas and the low-threshold access. Every Ford employee can submit an application via an app, adding their own drawing of the part they want or describing what they need it for.
"We are pursuing a start-up approach with short distances and little bureaucracy," said Oliver Färber, who, as plant manager of the engine plant, is also responsible for the area of the 3D printing centre. "The parts requested by the employees are then specially designed by the 3D printing team and can therefore be produced very quickly.”
For example, a door edge protector has already been created that is currently being tested on the line in final assembly and may be used at other stations in the future. An ergonomically improved installation aid for airbags is also being tested. Parts are already being 3D printed for the future production of the first e-model 'made in Cologne', with 1,800 impact protection devices currently being built for the new door transport system. They ensure that the doors are not damaged during transport to the line.
"I'm glad that we can open the 3D printing centre before the launch of our new e-model," said Rene Wolf, managing director, Manufacturing, Ford-Werke. "In this way we can gain valuable experience and already print thousands of parts". The most comprehensive transformation process in the company's history in Cologne not only affects the conversion of vehicle production to e-models, Ford also wants to promote digitization and Industry 4.0. "The 3D printing centre is a good example of this and another building block for the factory of the future, i.e. our vision of future production in the Cologne Electrification Center," said Wolf.
This time-lapse video shows how a holder for sheet metal samples is created in the Ford 3D printing centre.
NEW VEHICLES | ALL-ELECTRIC FORD CAPRI
COMMERCIALS | FORD TRANSIT COURIER
COMMERCIALS | FORD TRANSIT CUSTOM
COMMERCIALS | FORD RANGER
COMMERCIALS | FORD TRANSIT CONNECT
COMMERCIALS | FORD TRANSIT CUSTOM
COMMERCIALS | FORD TRANSIT CUSTOM
NEW VEHICLES | ALL-ELECTRIC FORD CAPRI
NEW VEHICLES